Qu’est-ce qu’une usine connectée ?
Animée par l’émergence des nouvelles technologies, l’usine connectée est tout simplement la combinaison entre le monde de l’industrie et celui du numérique. À l’intérieur, les machines, les produits et les collaborateurs forment un véritable réseau et échangent, interagissent et co-décident en permanence, pour plus d’efficacité et de productivité. Et tout cela, grâce à des technologies comme l’IoT, l’intelligence artificielle, la robotique, le big data, etc.
La plus grande différence avec les usines classiques, c’est que dans une usine connectée, les différents outils et postes de travail intégrés dans les chaînes de fabrication et d’approvisionnement sont interconnectés.
Il y a donc une communication continue et instantanée grâce à une solution M2M (machine to machine) dont l’installation repose sur un réseau sans fil à courte distance de type wifi, RFID, Bluetooth ou GSM. Cette solution permet d’une part, de recueillir tous types de données en permanence (débit et pression des machines, variations de température, usure des pièces, informations d’utilisation, statistiques de performances, etc). D’autre part, elle permet d’optimiser l’outil de production et de répondre à des enjeux incontournables pour les industriels :
- Produire plus rapidement
- À un meilleur coût
- Avec une agilité plus importante
Concrètement, comment ça marche ?
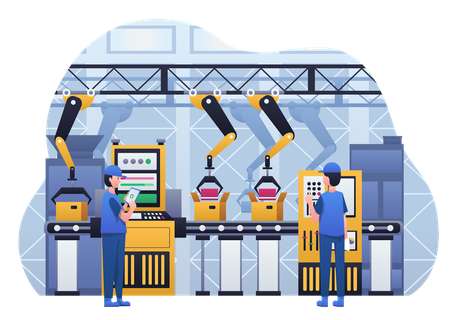
L’usine connectée repose sur des technologies clés. En effet, elle est comme une “mosaïque technologique” dans laquelle on retrouve différentes technologies fondamentales, comme :
- Internet des Objets (IoT). À l'intérieur d’une usine connectée, l’ensemble des données sont enregistrées par des capteurs embarqués sur des pièces ou sur des machines qui se trouvent dans toute l’entreprise. Ils sont alors capables de communiquer et d’interagir, souvent, grâce à des cartes SIM M2M (machine to machine) ou multi-opérateurs. Ces capteurs sont ainsi utilisés pour suivre en temps réel les cadences d’utilisation des machines afin d’optimiser la production. On parle alors de maintenance prévisionnelle. Ils permettent de prévoir les opérations de maintenance en anticipant les pannes. Par ailleurs, ils sont aussi d'excellents superviseurs énergétiques. Ils vont donc permettre par exemple, de localiser une fuite ou d’identifier la machine qui consomme le plus d’électricité. Le but étant de réduire les coûts liés à l’interruption involontaire de la production, mais aussi, d’allonger la durée de vie des machines en optimisant leur utilisation.
- Le Big Data. L’ensemble des données enregistrées par ces capteurs, font partie de ce que l’on appelle le Big Data. C’est-à-dire, un ensemble massif d’informations numériques issues de l’intérieur de l’usine. Ces données sont ensuite stockées, triées et analysées par l’Intelligence Artificielle (IA) afin de déclencher des opérations de maintenance et d’optimisation. L’IA va permettre d’exécuter instantanément des calculs complexes. Par conséquent, l’analyse des données s’effectue en temps réel, ce qui facilite la prise de décision pour les humains.
- Les cobots (les robots collaboratifs). Qu’il soit piloté en temps réel, configuré à l’avance, ou qu’il travaille à côté d’un humain, le robot collaboratif est fait pour collaborer avec le salarié. En fonction de sa programmation ou de ses extensions (capteurs de force, pinces, etc) il peut remplir énormément de tâches difficiles, dangereuses ou peu gratifiantes pour le salarié, lui permettant ainsi de gagner du temps !
- La réalité augmentée. C’est une technologie qui permet d’intégrer des éléments virtuels en 3D (en temps réel) au sein d’un environnement réel. L'intérêt est par exemple de guider les opérateurs de maintenance lorsqu'ils travaillent sur des machines (grâce à des lunettes numériques), ou encore d'accompagner les employés pendant le processus d'apprentissage.
- L’impression 3D. Technique de fabrication dite additive, elle a pour mission de rendre possible la fabrication de composants en un temps record et permet de gagner du temps aussi bien pour le prototypage que pour la production.
Par ailleurs, l’usine connectée n’est pas uniquement connectée dans les entrepôts. Elle s’ouvre également à son environnement, afin de mieux impliquer les partenaires et d’échanger avec tous ceux qui participent à la création, au développement et à la commercialisation des produits.
Ainsi, les avantages de l’usine connectée pour les entreprises sont multiples, ils permettent d'augmenter son potentiel de création de valeur tout en étant plus compétitif, plus moderne et plus proche du client.